Work Health Safety policies
Implement and monitor Work Health Safety policies, procedures, and programs to meet the legislative requirement
WORK HEALTH SAFETY POLICIES
FORMATIVE ACTIVITIES
Activity 1
- The impact of a workplace injury is wide reaching. Discuss in 50 to 80 words.
Efforts to improve safety must include strategies to deal with the effects of both the physical and socio-psychological environments on health. Workplace design layout and safety naturally impacts on the human component of work (performance). Interrelationships between workers and their environment (physical structures) have significant influences on productivity. Ergonomic design of equipment and machineries, workspaces which can be personalised for psychological and physical comfort or health; air circulation, appropriate lighting, workstations which meet health and safety standards etc., plus the free exchange of information in the workplace act to encourage skills development and enthusiasm for work. Giving due consideration to social structures within the workplace, and acknowledging that comfort and design of the workplace directly reflect corporate business vision, will naturally lead to greater workplace efficiency. To meet health and safety requirements both the physical and psychological interactions between workers and management and between workers and their work environment must be taken into consideration.
- How is the integrity (validity) of information ensured? Discuss in 50 to 80 words.
To properly support health and safety procedures in the workplace it will be necessary to locate and share information. Officers and workers need to know where to source health and safety information both internal (policies, records, procedures) and external (legislation and requirements). They also need to know how to check both sources and information for validity, reliability, consistency and currency and how to use information management systems to record, store and disseminate information effectively.
The most obvious source of reliable, external information about regulations, requirements and legislation is the relevant workplace legislative body in each state or territory. These bodies can inform enquirers of the legislation pertinent to their state/ territory and industry, and of their applications. Acts are the laws passed by parliament they often require amendment to keep them up to date. Copies of Acts and their amendments are available from government printing services. Amendments are printed in the latest copy of the Act, or may be obtained as separate documentation. The Act and regulations are also available on relevant websites.
As with all information, health and safety information should be verified. Prior to sharing information ensure its integrity. Is it reliable, valid, relevant, consistent, correct, sufficient and current?
Information might be unreliable for many reasons:
- information systems and storage might be inefficient, inadequate or incomplete
- person/s may be untrustworthy, or have different agenda from the enquirer or the company’s
- information might be out of date
- samples might be biased, insufficient or not random enough (or even too random)
- information might be improperly collected
Old, wrong, distorted or incomplete information is not useful. Use a variety of sources to correlate, compare and match information in order to determine consistency and validity. Familiarity with sources will help to assess reliability, providing checks and balances, and
pointing to contradictory or unusual information. However, do not rely on special sources of information due only to force of habit. Use the sources that are believed to be the best.
- List three sources of health and safety information in your state / territory.
WorkSafe, Western Australia Regulators, Training courses (TAFE) or Industry Pamphlets
Activity 2
- Why is it important that all workers have access to health and safety information? Discuss in 80 to 100 words.
New worker induction programs must include health and Information relevant to the new worker’s job specification. Because of effective induction, workers will be aware of the expectations placed upon themselves and other workers. Safety procedures, measures and requirements can be updated through in-house training, or through training delivered by expert consultants. This training should be reinforced at regular safety meetings, workshops, or at least as an agenda item at staff meetings.
It is a clever idea to conduct regular safety workshops and meetings with workers. This will accomplish a variety of goals:
- advertising to workers that officers and the company place a high value on worker safety
- providing workers with detailed information regarding company procedures and other safety requirements related to the work they do
- promoting team spirit and the notion that safety is really a team effort
- providing a forum for workers to ask specific questions
- creating opportunities to generate feedback from those who know what it is like to work with existing safety policies
Workshops or safety meetings need not be long and involved. Short, specific meetings are more effective. Interaction should be encouraged by asking for, and responding to, questions.
If the presenter does not have an answer to a question, they should find the answer and get back to the worker who posed the question. This will demonstrate their ongoing commitment to safety and to good communication processes. Providing some type of handout at all meetings or workshops gives attendees something to walk away with, to refer to, and to talk about.
- If a worker had made suggestions for improvement for the design, develop and management of health and safety in a company in which they worked, how could they go about having them ratified and implemented by senior management? Discuss in 80 to 100 words.
When improvements in attitude and work practice are noticed, they should be acknowledged. For example, a few days after a safety meeting on forklifts, a supervisor notices a formerly not so conscientious worker inspecting the safety devices on a forklift. Recognition and reward for
this kind of behaviour acknowledges the worker’s contribution to workplace safety and acts to encourage further improvement. Showing the team that actions have been noticed promotes team spirit and boosts morale.
- Before submitting strategies for the design, development and management of health and safety to senior management for approval, should the worker consult with the member of their team / department to get their input? Why / why not? Discuss in 100 to 120 words.
Yes, because thought the establishment good two-way communication processes in the workplace. Workers should feel that supervisors and managers are approachable, that worker problems and perceived issues will be taken seriously, that concerns will be addressed, that feedback regarding those concerns will be given and that promised action will be taken. They need to be able to trust supervisors and managers. Managers/ leaders in turn, need to demonstrate reliability and consistency. If workers are afraid to raise issues (including safety issues) or believe that their concerns will neither be taken seriously nor addressed, then they will soon come to resent management and will not perform at optimum levels. Workers must not be afraid or feel threatened when raising issues of importance
Activity 3
- Where might information about hazards and the outcomes of risk assessment and control result from? Discuss in 120 to 150 words.
Information about identified hazards and the outcomes of risk assessment and control might result from:
- examining legislation, regulations and codes of practice introducing changes or improvements to machinery, equipment and processes
- checking equipment before and during work consulting with work team members
- daily informal consultation with workers regular team meetings
- general housekeeping reviewing health and safety records including hazard reports, hazardous substances and
- dangerous good registers, injury records health and safety audits and audit reports
- workplace inspections
- List five ways that PCBUs can provide clear explanations to work teams about identified hazards and the outcomes of risk assessment and control.
PCBUs can use a variety of media to communicate the information including:
- emails
- team meetings
- informal discussions with workers
- posters
- signage at hazard site
- intranet sites
- risk registers
- presentations
- minutes of health and safety committee meetings
Activity 4
- What types of changes in the workplace would benefit from consultation between PCBUs and workers (or their representatives)? Discuss in 150 to 180 words.
- Workers identify hazards
- Assessing any risk
- Deciding on measures to control risks
- Implementing controls
- Reviewing the effectiveness of controls
- Reviewing and developing policies
- Investigating incidents
PCBUs must consult with all workers. including contractors, subcontractors, labour hire workers, apprentices, work experience staff and volunteers on health and safety issues. They must also consult with other PCBUs, so far as a reasonably practicable, if their duty of care overlaps with theirs.
- What are the benefits of consulting with workers about health and safety issues? Discuss in 120 to 150 words.
The intention of health and safety legislation is that the PCBU and the workers attempt to resolve health and safety issues which arise and regular consultative and participative arrangements facilitate this outcome.
Benefits include:
- Consultation and participation leads to ownership and support for initiatives.
- Consultation and involvement motivates workers to improve and to contribute to continuous improvement.
- Consultation indicates organisational respect for, and value of, worker opinions and experience.
- Workers are the people who know the job, the job conditions and the risks best.
Activity 5i
Explain the role of the HSR in each of these consultation procedures:
- Attendance at team meeting.
It involves negotiation on behalf of workers to improve conditions, resolve concerns and issues related to the work environment or workplace practice and report back to workers on results and outcomes, the same credibility requirements apply to HSRs as to HSCs.
- Early response to work suggestions, requests, reports and concerns put forward to management.
To investigate health and safety issues and complaints, issue a provisional improvement notice (PIN), accompany an investigator during an investigation inspect the workplace promote the health and safety at work of workers in their work group
- Requirements as specified in Commonwealth and state / territory legislation, regulations and codes of practice.
PCBUs and workers might need or choose to involve external parties in the consultation process. They might consult legislation and the bodies who incorporate the legislation to clarify compliance requirements. In some cases, qualified consultants with a specialised knowledge of health and safety might also be used to facilitate the process. For example, an engineer might be consulted on workable solutions for minimising the risk posed by some equipment in the workplace or audiologists might be consulted about best practice in the use of headsets.
Activity 6
- What strategies can PCBUs use to consult with workers on health and safety issues? Discuss in 80 to 100 words.
Consultation with workers enables problems and issues to be raised and discussed. Part of the role of HSCs and HSRs is to participate in monitoring and evaluation and to provide liaison between workers and management in any instances where worker concerns require resolution. This means that where problems are identified on the floor, workers can take their concerns to the manager who will pass them on to the HSC or HSR, or they can take them directly to the HSR. These representatives should undertake further investigation and consultation to evaluate the seriousness of the issues, and then negotiate with management to resolve problems.
- Health and safety issues raised through consultation should be dealt with promptly. Why is this? Discuss in 120 to 150 words.
Issues pertaining to physical or psychological problems which cannot be resolved through negotiation can be processed through arbitration. It is in the interests of the organisation to manage grievances and disputes within the workplace, as the conciliation process can be time consuming and costly, impact negatively on productivity and generate distrust and discontent amongst workers and other stakeholders. This an effective health and safety program will have specific and communicated grievance procedures. Worker grievances will be taken seriously, treated with respect and followed through to a satisfactory solution
Activity 7
- Create a meeting agenda template suitable for a HSC.
Meeting agenda
Fairy Solutions
Location: 26 Edgehill St / Perth – WA
Date: 09/06/2017
Time: 14:00
Agenda details:
- During this meeting, we will about safety and best procedures with the tools and the vehicle.
- Each employee shall bring some ideas about how to prevent accidents.
- Everyone should get some literature about Safety and healthy in work environment
- Best procedures.
- The first Topic will about the use of grease before using the especial heads in the jackhammer.
- Second, we will discuss about the misuse of the leads and the mess inside the trailers
- Vehicles and responsibility.
- Another topic in discussion will be about the chips, scratches in the uses and the broken windscreen.
- Finally, we will point each one that had responsibility in these incidents and then get them to sign some writing warnings if the incidents happened with bad use of the tools or the cars.
- Create a meeting minute template suitable for a HSC.
Minute meeting
Fairy Solutions
Location: 26 Edgehill St / Perth – WA
Date: 09/06/2017
Time: 14:00
Present: Thaisa, John, Gabriele, Debora
Agenda items
- In the meeting we’ve got some important ideas like using better ways to put the tools inside the utes. That could be resolved with a use of crane.
- Another idea is the use of some feature that could tie the tools inside the ute preventing falls.
- The jackhammer must be greased to prevent it to get broken
- About the bad use of the cars it was decided that the drivers will be replaced.
Action items Owner(s) Deadline Status
[Crane + Feature to tie] [Thaisa] [22/06/2017] [Late]
[Jackhammer procedures] [Debora] [24/06/2017] [Complete]
Activity 8
- What is a training needs analysis and how can it be conducted?
A training needs analysis (TNA) is the formal process for determining training needs, that is, the gap between the required skill and knowledge level of workers to enable them to perform their tasks and the current skill and knowledge level of workers.
The TNA process provides organisations with an accurate overview of workforce training requirements to enable them to identify training needs within the organisation. They also assist with training vendor selection and budgeting, and can help to improve worker retention levels and overall worker satisfaction. Before spending time and effort conducting a TNA, organisations should make sure training will provide a solution.
- What tools can be used to identify the skills a worker needs?
Useful tools to help identify knowledge, skills and standards include:
- industry standards
- competency standards
- training and assessment records
- licence requirements
- discussion
- skills auditing
- benchmarks
- job descriptions
- standard operating procedures (SOPs)
- policy and procedure manuals
- existing training programs
- What are the 6 steps in developing a training program?
- Analyse then survey results
- Create a worker training profile
- Develop a training profile
- Communicate the training development plan to all employees
- Implement the training
- Evaluate the training effectiveness
Work Health Safety policies
Activity 9
Your team is concerned that they have insufficient knowledge / understanding of safety procedures and legislative requirements in your workplace. They also feel that the incidence of accidents in your section is higher than it should be. They have asked you to submit, to senior management, a proposal for a formal health and safety training program.
- What information would you include in the proposal and how would you encourage senior management to support this initiative? What procedures would you follow in gathering data and information to support your proposal? How likely is it that this or similar proposal would be accepted in your workplace?
The information included in the proposal should include what the training program might cover, (health and safety responsibilities and roles, hazard and risk identification and reporting procedures). The senior supervisor should be presented with the team concerns and reports of increased incidence of accidents in given section. Proposal should be supported with statistical analysis of incidence reports and team TNA evaluation such as formal assessment, or consultation between managers, supervisors, HSCs, HSRs and workers. Also, the senior management should be made aware of their legislative and regulatory requirements. It is very likely that this or a similar proposal would be accepted in the workplace as team feedback underlines an apparent need for it.
- What critical information must be contained in a new worker induction program?
- Health and safety training as necessary dependent on job role
- Introduction to important staff
- Tour of the building, pointing out fire exits, bathrooms, meeting rooms, boardrooms, useful offices such as IT support staff, administration staff etc.
- Specific job task training to ensure that workers have the skills and knowledge they need to complete tasks in a competent and safe manner
- Why is only providing induction training and no follow-on training unsatisfactory?
It is unsatisfactory to provide only induction training and no follow-on training because a person might not learn what is needed. Follow-up training will ensure that the trainee get the right support and keep in touch with the trainer for 6 months – 1 year. Support of trainees after training refers to mechanisms that allow the training organization to respond to questions, doubts, or problems that the trained providers experience in the service delivery environment. Refresher training is one mechanism for supporting trainees long after the training event.
Work Health Safety policies
Activity 10
- What are the benefits of evaluating training to both workers and the organisation?
Measures of success on both individual and organisational levels are an essential element of training/ learning. Monitoring and evaluation processes ensure that training achieves its objectives, the learning outcomes are met and the expected benefits are achieved. Training and learning should be an integral part of the organisation’s quality processes, therefore, it is necessary to measure and evaluate training success to determine, as far as is possible, the cost-effectiveness of training (return on investment) and the degree to which training contributes to organisational success. This applies to all the training received by workers, including health and safety training.
- When evaluating health and safety training, how can you determine the appropriateness and effectiveness of training?
I can determine the effectiveness through visual confirmation, in which learners demonstrate their knowledge by performing a role-play. Or the learner could record a video completing the task and send to the trainer. Another way is asking the learner to teach the same task to someone else. This concept not only engages employees to teach and learn from each other, it also gives training managers the ability to measure how well concepts are being implemented within the organization. Or just compare and map against past performance in given areas, allowing reasonably accurate evaluation.
- What should be evaluated in relation to a health and safety training program?
- The realism of the projected goals.
- The clarity of learning outcomes, information presented and the assessment procedures.
- Whether trainer and trainee expectations were identified, expressed and met.
- Was the material presented at a suitable level, and was it challenging yet manageable?
- Was the training content interesting, stimulating and relevant?
- What effect has, or will it have, on productivity/ productivity measures?
- What attitudinal changes can be expected because of the training?
- Was it cost-effective?
- Were the facilities, resources, consumables and environment conducive to effective
- training?
- Did the trainer/s demonstrate an in-depth knowledge of the subject matter?
- Were the methodologies and techniques used suited to the adult learning situation?
- Were individual needs and preferences catered for and were all relevant variables
- considered?
- Was communication and training delivery clear and understandable?
- Were materials and tools used well and suited to the training and to the trainee needs?
- Were participants given appropriate opportunities to contribute to the training, to be
- involved and to practice new skills?
- Were the participants satisfied with the training/ learning?
- Will the new learning provide participants with transferable skills?
Work Health Safety policies
Activity 11
Your organisation has identified an increase in injuries to workers who use the new plant. You are responsible for training in the area where the injuries occur. Your rate (for the exercise) is $360 per day. A training needs analysis concludes a training program will reduce the injury rate.
Consider:
- The training needs analysis will take two days, including reporting to management
- It will take you five days to develop the training program
- You can get a good training video at coast of $375
- You will need to hire a TV / video for each session, cost $120
- Handouts will cost $12 per participant
- Management wants you to conduct the training at a venue that costs $195 per day
- Catering is available, $25 per participant per day
- You will deliver the training
- Lost production is costed at $320 per day per participant
You will train 20 workers in five groups. Each course runs for one day. Administrative support works out at $28 per participant.
Calculate the coast for training.
Training Cost | |
Trainer Cost (12 Days) | $ 4.320 |
TV / Video hire (5 days) | $ 600 |
Training video (1 unit) | $ 375 |
Handouts (20 workers) | $ 240 |
Venue (5 days) | $ 975 |
Catering (20 workers) | $ 500 |
Lost production (20 workers) | $ 6.400 |
Administrative support | $ 560 |
Total | $ 13.970 |
Activity 12
- What is the difference between a risk and a hazard?
A hazard is any source that has the potential to harm life, health, property or the environment. A risk is the chance of something harmful occurring—the likelihood that harm will occur as a result of a hazard.
- Create a 1 page checklist for a manager / supervisor to assist them with the identification of hazards.
- Conduct regular, well-organised, documented and recorded safety inspections of work areas and work practices;
- Objectively and regularly analyse and evaluate procedures and systems of work
- Investigate all accidents, injuries, incidents and near miss events immediately after the event (to keep accurate records)
- Inspect all additional items purchased and installed to determine potential hazards
- Implement waste disposal and recycling procedures which will ensure both worker and environmental safety
- Ensure that purchase orders contain specifications about health and safety considerations for new plant and equipment
- Ensure workers understand correct and safe working and operating practices
- Respond promptly to concerns or enquiries made by workers – acting on, and providing prompt feedback regarding issues raised, will encourage workers to report hazards and become more safety conscious
- Conduct or organise regular health and safety training, coaching or mentoring for workers
- Encourage workers to list and report hazards of which they are aware – hazard identification and reporting is everyone’s responsibility
- Consult personally with workers to discuss any problems they have in their work area
- Ensure that worker job descriptions and KPIs state health and safety responsibilities about job requirements
Work Health Safety policies
Activity 13
- Why should organisations have comprehensive risk assessment procedures?
Because accurate recordkeeping is essential. The records will become part of the periodic risk assessment system, providing valuable information for comparisons, decision-making, verification of past actions and for demonstrating legislative compliance.
- A hazard has been assessed as being unlikely, but would have major consequences. Using the risk matrix, identify the risk and what it means to the organisation.
Risk assessment matrix:
Likelihood(Exposure) | Severity / consequence | ||||
Insignificant | Minor | Moderate | Major | Catastrophic | |
Almost certain | High | High | Extreme | Extreme | Extreme |
Likely | Medium | High | High | Extreme | Extreme |
Possible | Low | Medium | Medium | Extreme | Extreme |
Unlikely | Low | Low | Medium | High | Extreme |
Rare | Low | Low | Medium | High | High |
High Risk. It means that it is unlikely to happen but if it happens it would have major consequences.
- What are the factors that impact upon the severity of an incident?
Factors affecting severity include:
Internal
- the number of people who might be affected in one incident
- special characteristics of the persons involved
- concentrations of chemicals etc
- volumes of materials
- speed of projectiles and moving parts etc
- heights and distances
- weights
- forces and energy values
In terms of environmental impact, factors affecting severity include:
- the size of the environmental release
- the affected medium—land, air or water
- concentration of materials
- containment
- degree of difficulty with the clean-up
- the number of people affected (both company personnel and external persons/ stakeholders)
- degree of permanent damage or lasting effects
These factors could indicate a relationship between accidents, and human physical conditions and occupational qualities. They can also help identify the groups of workers who are highly prone to accidents. Furthermore, they allow mitigation strategies to be specifically targeted using workers’ characteristics as preliminary factors. These characteristics are believed to be influential in workers’ behaviours on a workplace, which could be unsafe in certain circumstances. Personal and work characteristics combined with the working environment are believed to influence the creation of a hazardous environment that could be triggered by different mechanisms that cause an accident.
Work Health Safety policies
Activity 14
- Give an example of each of the following types of controls for managing hazards.
- Elimination
The hazard is removed from the environment. Design processes factor in controls and specifications to eliminate hazards (egg. noise or vibration control, enclosed machinery). The task is eliminated from the process.
- Substitution
In some cases, it might be expedient to replace materials or processes associated. With the risk with something less hazardous (the replacement of a toxic material or substances with another that does the same job but is less toxic). For instance, sandstone grinding wheels containing silica (silicosis risk) have been largely replaced by wheels made from an inert, less harmful, artificial abrasive called aluminum oxide.
- Engineering
Equipment, work processes, tasks, machinery can be redesigned to reduce or eliminate worker risk (mechanical lifting devices versus manual handling risks).
- Administration
Administration processes can be used to adjust work conditions and redesign jobs to limit the risk (for example, shared jobs or reduced time attending to a particular activity can limit the risk of exposure to hazards—chemicals, difficult processes, isolation, sunlight, repetitive strain, etc.). Administration can also be called upon to provide signage, instruction manuals, advice and training. Training is a popular control method but should accompany other more preferred controls and not be relied on as the sole control.
- Personal Protective Equipment (PPE)
This is the least preferred option in hazard control—a last resort. The objective of health and safety is to make workplaces safe—to eliminate hazards, not to make workers work around hazards. PPE in use at a workplace indicate the need to revisit risk management on a programmed basis. If exposure cannot be prevented or reduced by ways other than the use of PPE, the PCBU must ensure that persons who may be exposed are supplied with and properly instructed in PPE use.
- How often should risk assessments be conducted?
The risk assessment must be conducted in each different site as soon as the job begins (in my company its everyday) and as soon as a significant new hazard appears (When the company hire new tools, when someone gets sick, when the rate of accident raises).
Work Health Safety policies
Activity 15
You are the safety supervisor at a commercial construction company. The company employs 12 administration personnel, 18 construction personnel and 60 construction subcontractors.
The workers who work on-site face a changing work site each day and are often working with people from other companies. Three months ago you were alarmed at the n umber of back injuries being reported and introduced new procedures that were aimed at ensuring heavy items were lifted in accordance with the legislative requirements of your state / territory and work requiring bending for long periods was minimised. You provided a toolbox meeting to inform the workers of the new procedures and techniques. You now need to evaluate this strategy to determine whether it has met you aim of reducing back injuries.
Data | Reason | Data source |
Company back injury rates | Core data. | Injury reports. |
Company near miss for back injury rates | Leading indicator for actual back injuries. | Near miss reports. Anecdotal conversations with key workers. |
Company overall injury rates + causes | Determine whether there are other reasons for a change in rate. | Injury reports. |
Company near misses | Leading indicator for other injuries. | Near miss reports. Anecdotal conversations with key workers. |
Industry benchmarks on back injury rates | Establish a norm for performance. | Employer association. State jurisdiction. |
Using the supplied information, develop a procedure for systems evaluation that covers:
- Inclusion of external data in the evaluation process
- External input into the evaluation process, eg stakeholders
- How identify areas for improvement will be documented and actioned
- How top management will be involved in the review process
The evaluation procedure will need to include external data:
- safety committees, suggestions, recognizing/rewarding
The external input into the evaluation process will be held by:
- engineering, management, PPE, interim measures, maintenance
The identifications for improvements will be documented beyond:
- inspections, observation, surveys, interviews
The Top management will be involved in three different ways:
- Leading, following, managing, planning, funding
- Providing: orientation, instruction, training, personal experience
- Judging effectiveness of conditions, behaviours, systems, results
Work Health Safety policies
Activity 16
- Why is it important to keep health and safety records?
Because the records will be available to support improvement initiatives, design and develop new policies and procedures, and act as proof that the organisation is upholding its responsibilities to workers and legislation. It also need to be available in the case of worker’s compensation claim or as evidence in a litigious action. In this way, health and safety is integrated into organisational systems.
- Name three health and safety records that must be kept by every organisation.
Incident records, The first aid register and The register of all injuries.
- If you are the health and safety representative of a company, how could you ensure that the workers you represent are aware of the recordkeeping requirements?
Beyond manuals, guides, handbooks or instructional lists, accident report forms, and complaint/grievance procedure forms. These documents need to be registered in some way (electronically, or, hand-writing) to make sure the documents were filled in, named and stored in non-restricted folders, or network locations.
Work Health Safety policies
Activity 17
- A workplace employs 75 workers who work a total of 150.000 hours in a year. They experience eight lost time injuries for the year, resulting in 65 days off.
Calculate the following:
- Frequency rate.
FR- 8*1000000/150000 = 53.33
- Incidence rate.
IR- 8*1000/75 = 106.66
- Average lost time / severity rate.
SR- 65/8 = 8.125
Provide your workings.
- You are required to present these statistics to your next senior executive weekly committee meeting. Describe how you will present this information. Include copies of any graphs or tables that might be relevant.
The company employees 75 workers, the total of working hours a year is 150,000. The total of lost time injuries for this year is 8 (injuries that have resulted in the loss of at least one entire shift). These results in a total of 65 days off.
The frequency rate for that year is calculated as follows:
FR = Lost time injuries times 1,000,000 divided by the total number of hours worked.
That is:
FR = (8 X 1,000,000)/150,000
The frequency rate is: 53.33
The incident rate for that year is calculated as follows:
IR= Lost time injuries times 1,000 divided by the number of wages earners.
That is:
IR = (8 X 1,000)/75
The incident rate is: 106.66
The severity rate for that year is calculated as follows:
SR = Number of working days lost divided by the number of occurrences in the period.
That is:
SR = 65/8
The severity rate is: 8.125
Work Health Safety policies
SUMMATIVE ASSESSMENT 1
Question 1
What are the key aspect of health and safety legislation?
Legislation places a health and safety duty on these individuals—who are described as officers—to require them to take steps that will support a health and safety culture, accountability and the allocation of resources and policies.
Officers are not appointed positions. Whether someone is an officer or not will depend on. Whether they make, or participate in making, decisions that affect the whole or a substantial part of the PCBU. Officers are generally at a senior level within the organisation or business. There is no opting out of the duty.
Health and safety legislation has contributed to a notable change in the understanding of health and safety responsibility issues. Where previously it was the workers fault if they were involved in accidents, it is now recognised that the PCBU has a duty of care for all workers and that the PCBU is responsible for providing a safe and secure working environment. PCBUs are obliged to understand their liabilities and are compelled to look at their safety records because workers’ compensation premiums are tied to the compensation record in each industry.
Safe Work Australia (the national policy body) advocates that the key to improving Australia’s economic efficiency is to preserve a quality of lifestyle in a safe and healthy environment (Schuler et al. 1992). It is now accepted that responsibility for health and safety issues must be placed with the parties who directly affect workplace conditions PCBUs and workers, manufacturers, importers and suppliers. The underlying principle of legislation is self regulation and recognition that health and safety problems can only be avoided by making changes to the workplace, work practice and work conditions.
Work Health Safety policies
Question 2
What processes or procedures might an organisation use to identify hazards and monitor risk control procedures?
Information about identified hazards and the outcomes of risk assessment and control might result from:
- examining legislation, regulations and codes of practice
- introducing changes or improvements to machinery, equipment and processes
- checking equipment before and during work
- consulting with work team members
- daily informal consultation with workers
- regular team meetings
- general housekeeping
- reviewing health and safety records including hazard reports, hazardous substances and dangerous good registers, injury records
- health and safety audits and audit reports
- workplace inspections
About the risk control procedures, the hazards should be subject to identification, assessment, evaluation, control and monitoring and review. Identification of hazards and control include:
- conduct regular, well-organised, documented and recorded safety inspections of work areas and work practices
- objectively and regularly analyse and evaluate procedures and systems of work to identify hazards which may otherwise be overlooked
- investigate all accidents, injuries, incidents and near miss events immediately after the event, in order to pinpoint contributing factors-keep accurate records
- inspect all new items purchased and installed to determine potential hazards
- implement waste disposal and recycling procedures which will ensure both worker and environmental safety
- ensure that purchase orders contain specifications regarding health and safety considerations for new plant and equipment
- ensure workers understand correct and safe working and operating practices respond promptly to concerns or enquiries made by workers, whether they are made directly, or through health and safety representatives–acting on, and providing prompt
- feedback regarding issues raised, will encourage workers to report hazards and become more safety conscious
- conduct or organise regular health and safety training, coaching or mentoring for workers encourage workers to list and report hazards of which they are aware-hazard
- identification and reporting is everyone’s responsibility
- consult personally with workers to discuss any problems they have in their work area
- ensure that worker job descriptions and KPIs state health and safety responsibilities regarding job requirements
Work Health Safety policies
Question 3
Why is it important to provide information to work teams on the relevant heath and safety legislation, the organisation’s health and safety policies, procedures and programs, and any identified hazards and their control? Discuss.
New worker induction programs must include health and Information relevant to the new worker’s job specification. Because of effective induction, workers will be aware of the expectations placed upon themselves and other workers. Safety procedures, measures and requirements can be updated through in house training, or through training delivered by expert consultants. This training should be reinforced at regular safety meetings, workshops, or at least as an agenda item at staff meetings.
It is a good idea to conduct regular safety workshops and meetings with workers. This will accomplish a variety of goals:
- advertising to workers that officers and the company place a high value on worker safety
- providing workers with detailed information regarding company procedures and other safety requirements related to the work they do
- promoting team spirit and the notion that safety is really a team effort
- providing a forum for workers to ask specific questions
- creating opportunities to generate feedback from those who know what it is like to work with existing safety policies
Workshops or safety meetings need not be long and involved. Short, specific meetings are more effective. Interaction should be encouraged by asking for, and responding to, questions.
If the presenter does not have an answer to a question, they should find the answer and get back to the worker who posed the question. This will demonstrate their ongoing commitment to safety and to effective communication processes. Providing some type of handout at all meetings or workshops gives attendees something to walk away with, to refer to, and to talk about.
Work Health Safety policies
Question 4
Explain the importance of effective consultative mechanisms in managing health and safety risks and describe what they entail. Discuss.
Consultation is the fundamental element of a positive approach to health and safety in the workplace though consultation, managers and supervisors can become more aware of hazards and health and safety issues experienced by workers, workers can also provide suggestions about how to solve health and safety problems.
Consultation is about sharing health and safety information with workers and providing them with an opportunity to respond and contribute to health and safety issues that affect them. Health and safety legislation requires effective consultation between PCBUs and workers.
Consultation and participation is specifically referred to in Commonwealth and state legislation and includes directives such as requirements for PCBUs and workers to reach agreements on arrangements in the workplace that relate to health and safety dispute resolution mechanisms protection for worker consultation, participation and representation rights PCBUs should consult with workers before changes are made in the workplace that might affect health and safety including when:
- workers identity hazards
- assessing any risk
- deciding on measures to control risks
- Implementing controls
- reviewing the effectiveness of controls
- reviewing and developing policies
- investigating incidents
- changing work organisation, practices and procedures
- introducing modern technology, machinery, equipment, substances and processes to the workplace
- identifying health and safety training needs
- reviewing job design and job redesign
- changing work layout and conditions
Work Health Safety policies
Question 5
Explain how the hierarchy of control applies in the work area. Discuss.
- A hierarchy of control has been developed that lists control measures in order of effectiveness:
- Eliminate the hazard—remove noisy equipment.
- Substitute the hazard with something of a lesser risk—vacuum rather than sweep.
- Isolate the hazard—place barriers around a spill.
- Use engineering controls—use a trolley to move heavy loads.
- Use administrative controls—instruction and training.
- Use personal protective clothing—hearing and eye protection.
Multiple controls can be used. For example, cutting tools can be protected by guards that prevent debris from endangering workers, but this control can be augmented by an administrative control (a safe work procedure) and mandated wearing of PPE.
The hierarchy of control should provide the guidelines when planning for safety and designing hazard and risk controls. When implementing workplace changes, refer to the hierarchy to ensure that new processes and procedures will not increase worker risk and that they will comply with industry standards and safety requirements. Develop organisational procedures that enable selection of and maintenance of control measures in accordance with the hierarchy
Compliance with the hierarchy assumes that resources will be available to implement safety procedures as and where they are required and that inadequacies in current risk control measures will be mapped against the hierarchy to determine where improvement can and should be made. Where measures are found to be inadequate, new measures and controls should be designed and implemented, in consultation with workers and their managers or supervisors.
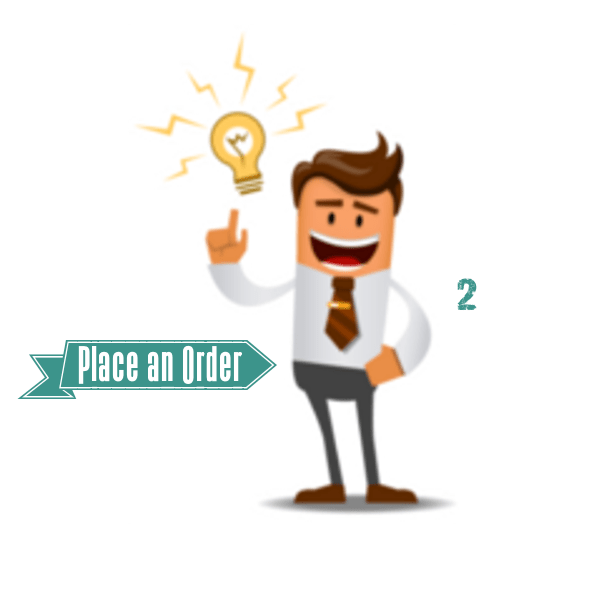